Partner
DeFelsko
Pore & defect detector
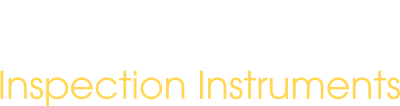
Pore & defect detector
Benefit
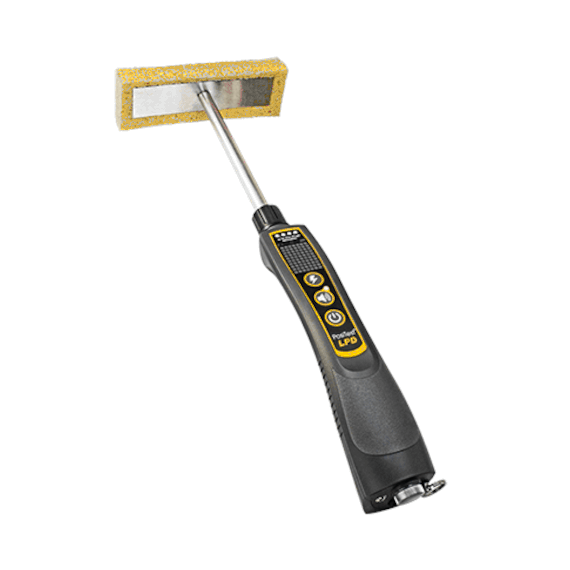
Use of pore & defect detector
Once a protective coating has been applied, it must be ensured that there are no defects or interruptions that expose the underlying substrate. Small areas of thin or missing coating, known as "pinholes" or "voids", can become centres of corrosion and drastically shorten the life of a protective coating system. A pinhole or flaw detector is a non-destructive instrument for detecting discontinuities in a coating system, including flaws, pinholes and cracks. Other names are porosity detector, continuity tester, discontinuity tester, spark tester and jeep meter.
DeFelsko offers two types of porosity/hole testers: Low voltage (wet sponge tester) and high voltage (spark tester).
Measuring device
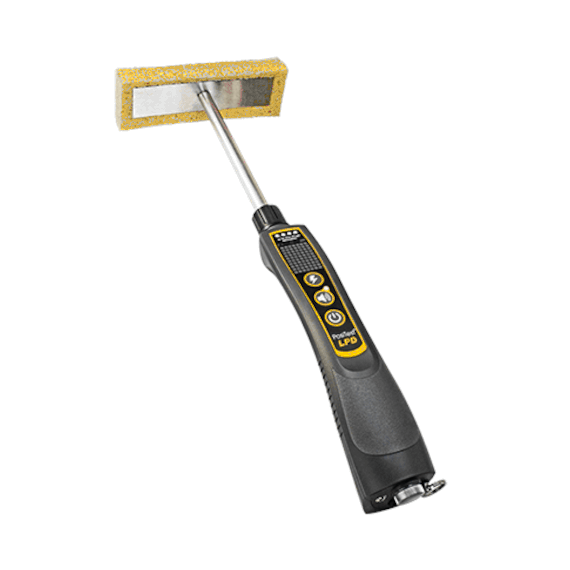
PosiTest LPD
Low-voltage pinhole detector
The PosiTest LPD Low Voltage Pinhole Detector uses a wet sponge to detect voids, pinholes and other discontinuities on metal and concrete substrates with four regulated voltage output options for coatings up to 500 µm (20 mils).
Complies with standards ISO 14654/29601/8289-A, ASTM G62/G6/D5162, BS7793-2, NACE TM0384, SP0188, AS3894.2, JIS
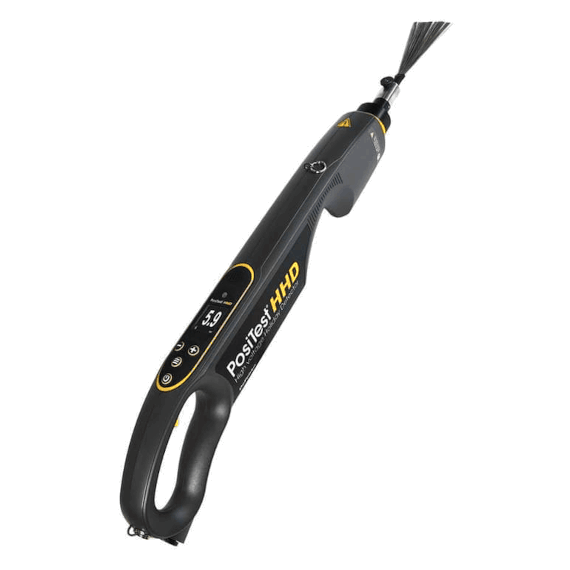
PosiTest HHD
Pulsed high voltage detector Defects
The PosiTest HHD High Voltage Flaw Detector utilises pulsed DC technology to detect flaws, pinholes and other discontinuities on metal and concrete substrates. User adjustable voltage range from 0.5 to 35 kV.
Complies with ASTM D4787/D5162/D6747/D7953/G62, ISO 29601, NACE SP0188/SP0274/SP0490, AS3894.1
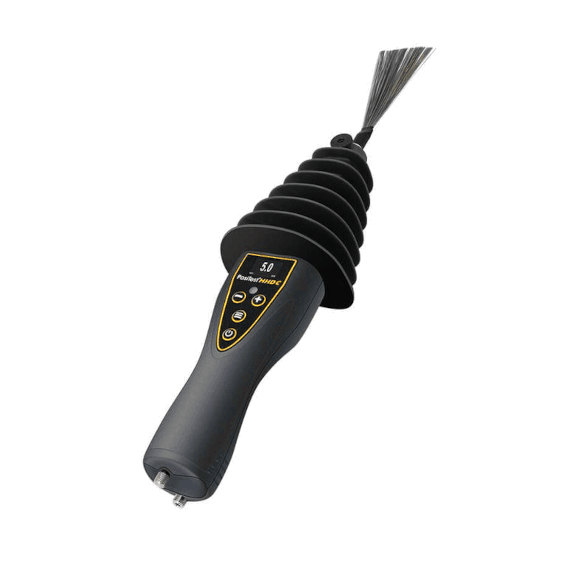
PosiTest HHD C
Continuous high voltage Fault detector
The PosiTest HHD C High Voltage Defect Detector utilises continuous DC technology to detect defects, pinholes and other discontinuities on metal and concrete substrates. User adjustable voltage range from 0.5 to 30 kV.
Complies with ASTM D4787/D5162/D6747/D7953/G62, ISO 29601, NACE SP0188/SP0274/SP0490, AS3894.1